A feature in our 2021 Late Summer issue, written by Kathleen O’Keefe.
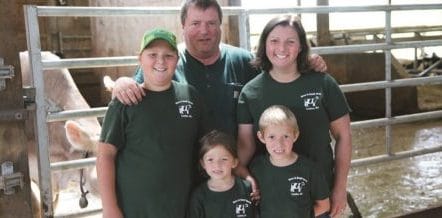
Goldilocks would feel right at home at Bree-Z-Knoll Farm, a family-run dairy operation located in the rolling hills of the Pioneer Valley in north-central Massachusetts. Over the past decades, the milking herd size has grown from 40 to 190 cows, and then back to the current 120 head – mirroring Goldilock’s exploration of the Bears’ house – ‘This one is too small. This one is too big. This one is just right!’
Warren and Sandie Facey started the herd in the 1970s, when they purchased their first cows for their children, Lisa, Scott, and Randy to show in 4-H. Over time, they grew their numbers to 40 cows that were managed with a rotational grazing program. In 1997, they were founding members of the Pioneer Milk Marketing Cooperative, which saw the introduction of a successful, local brand of milk (Our Family Farms label) eventually found on store shelves throughout the region.
By 2000, their youngest son, Randy, had taken over the day-to-day operation of the farm and he started to increase the size of their herd, which consisted of primarily Holsteins with a smattering of Brown Swiss. His wife, Angie, grew up southeast of him in Spencer, MA on her parents’ farm with their Royal Crest Holsteins. After receiving her degree from Penn State University, Angie began her career as a dairy nutritionist in 2001. She met Randy at his farm as a new customer in May, 2002 and they were dating by June! The couple married in 2004, and Angie joined the farm partnership. With that, they doubled their herd size with the purchase of her family’s milking herd that same year.
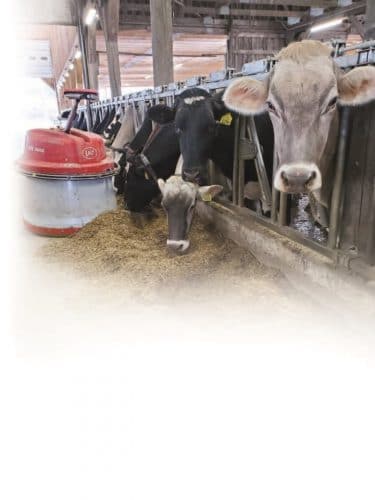
Like many young couples farming together, Randy & Angie wrestled with the balance of having enough cows to meet financial needs, but not so many that cow comfort and family life were compromised. “With the addition of my family’s herd, we really started to tax the facilities at the farm,” Angie comments. “We had to have our heifers raised at my parent’s farm, and we were always feeling pressed to get everything done for the cows.” They started formulating plans for a robot barn set up in 2015, with the initial thought of building a 240-cow, 4-robot facility at a site six miles south of the home farm in Greenfield, MA. That plan did not work out, so they moved on to retrofitting the home farm in Leyden, where they would milk fewer cows with two robots.
Those plans got pushed forward early in 2018 when their main herdsman quit, and Randy sustained vast injuries after a March car accident. All of a sudden, it became clear that the herd had to get smaller in order to do a better job with the cows. Construction on a new milk house and the section of the barn that would house the robots began in August 2018. They sold about 60 cows and about 45 open heifers to get down to a more manageable size.
After that, they aggressively dried up a large group of cows early, and when the two Lely A5 robots were booted up in December 2019, they were down to milking 88 cows. “The barn wasn’t complete when the robots started, but we just had to get underway,” notes Angie. “We completed the expansion of the free-stall barn last summer. We also installed Discovery robot manure scrapers as well as a robotic feed pusher that runs once an hour, 24 hours per day, and we couldn’t be happier with how the transition went. We worked hard at shaping and cutting down the herd numbers ahead of time, and we didn’t have to cull anything because of the shift over to robots.”
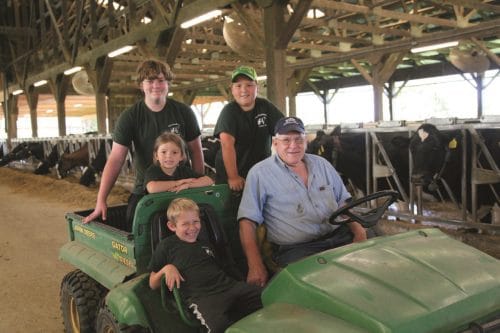
Unforeseen in this timeline was, of course, the COVID situation. “We went into the pandemic with a low volume of milk leaving the farm. Unfortunately, this volume was used as a base during the brunt of covid right when we were starting to see increased milk production. Dairies all over the Northeast were forced to dump milk or ship it for a charge” explains Angie. “Because of the pandemic and food chain issues, the state of Massachusetts developed a food security infrastructure grant program. With a large grant from that, we are currently building an on-farm milk processing plant that will exclusively bottle the Our Family Farms label. We’re converting our pre-fresh barn to the processing system and hope to be up and running by November.”
Randy will be in charge of the processing side of the plant and is interested in product development. He hopes to roll out flavored milks as one of the new products that Our Family Farms will introduce to the marketplace this fall. That, in addition to overseeing the finances, robots, cropping, feeding, and equipment maintenance on the 550-acre operation.
Angie is the herd manager at the farm, while also being employed off the farm as the General Manager of Pioneer Milk Marketing Cooperative. She will become the co-manager of the milk plant when it is operational. She works closely with employees Ashley Owen and Samantha Vanos overseeing all the animals, including cow, heifer and calf health, breeding decisions, and record keeping. Angie is appreciative of the help they have on the farm. “Ashley is the main person working with the cows all day, and Sam does evening chores and other valuable work around the farm all week. They both excel at caring for the cows. They’ve both been with us over two years. They milked in the old step-up parlor, have gone through the robot transition, and are excited for this new venture.
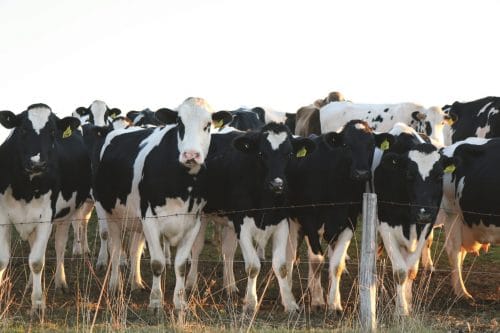
ANGIE FACEY
“We’re proud of the facility we’ve built. We are finally at a point where we have the right spaces for all of the cows groups we need. Having the calving pens at the end of the robot barn has allowed us to reduce the number of transitions the cows have to make to get to the milking barn. The cows are comfortable and not overcrowded. We’re proud of our employees who care for our cows with the same care and concern that we do. We are lucky to have such good people working for us,” enthuses Angie.
Randy’s sister, Lisa Moore, lives next to the farm and feeds calves six mornings a week to help out. Lisa and her kids are the ones that like the Brown Swiss best and use those heifer for their 4-H projects.
Angie admits she is a Holstein person through and through. She and Randy’s kids are the third generation on the farm – Ethan (11), Mason (6), and Charlotte (5) – and she makes sure they have Holsteins on the halter at the fair! She loves the fact that Ethan is now showing ‘G’ family members that trace back to the Goldie cow – Angie’s first registered 4-H cow. The kids enjoy accompanying Angie when she makes her evening pass through the barn to check on the cows every night.
The 120-cow herd has improved production since the shift to robots. Up to a 90# per day average, the RHA is about 27,000 lbs of milk with a 4.0% butterfat and 3.1% protein and a SCC count consistently under 100,000. They pasture as many animals as they can in the spring, summer and fall, including the far-off dry cows, and heifers pregnant over 100 days. The calves move from individual hutches to super hutches before moving into the heifer barn at about five months of age.
Angie, an impeccable record keeper, has all the information she wants and more from the system. “We’ve never had so much information per cow as now. We can check things on an app on our phones or on the computer. It tracks their movement, their production – because of that, sometimes I think we know they’re sick before they do! We use way more aspirin than we did before because we are catching things so much earlier, we usually don’t have to resort to more extreme and more expensive medicines. It’s just easier to care for them
– we can route cows automatically into the sick pen for example, so that they get immediate care.“
With all the on-farm changes in the past few years, regular classification had been put aside for awhile, but Angie was delighted to have four new Excellent cows when the classifier stopped in to score the herd last June. They breed for higher type, good udders and feet & legs, but also want the correct rump angle on their cows. “I don’t use any negative production bulls, but I don’t worry if they’re not high production bulls. We have good quality feed and are happy with how we can get our cows to milk. We’re using Angus on our lower end cows and heifers, so I’m spending more on better semen for the cows we are breeding to Holstein sires. We use a mix of genomic and proven sires in the herd,” Angie notes.
They like to show at the local fairs, and at the 4-H show at the Big E. They have an arrangement with a number of local 4-H kids that want to borrow heifers for the summer show season that works well for everyone.
It’s clear that the Faceys love what they do and they love their cattle. They’re active in community outreach, whether it’s having state lawmakers visit their operation or participating in the local library’s Ag Day. The Our Family Farms cooperative meets the public at farmers’ markets and always is looking for a chance to have a calf available to pet and to establish personal connection with the local consumer. The Faceys attention to detail and care for their herd and their land led them to be named the Massachusetts Greener Pasture Award winner for 2021.
For Angie, the days ahead are filled with excitement. “We’re blessed to live on our beautiful farm and raise our family here. We’re proud of the ingenuity that has kept us alive in this tumultuous dairy economy. We are incredibly grateful that Massachusetts has recognized the importance of ‘home-grown’ food and has given us the opportunity to build the milk plant. We thought the robot facility was life-changing, but this plant will also be life-changing!”
For Angie, one of the best features of building the processing plant is that she can relocate her office to the farm and be closer to their cows. “It just makes me so happy – all of the improvements and developments we’ve done – we finally have all the room we need for maximum cow comfort and care!” It seems that the Faceys, like Goldilocks, have landed on the operation size that is ‘just right’ for them!